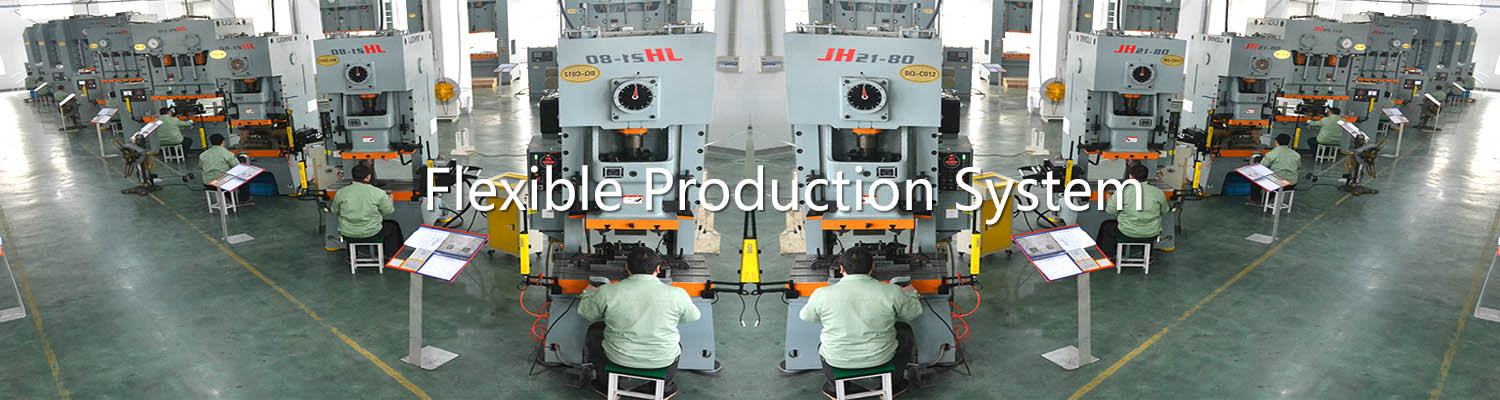
New Products
Carbide Hexagonal Dies Established in 1999, Zhu Xun Precision Mold and Die Factory meets customers’ rapid and large demand with its profound knowledge of tungsten carbide, lates... more
Industrial Carbide Wear Parts 2 Established in 1999, Zhu Xun Precision Mold and Die Factory meets customers’ rapid and large demand with its profound knowledge of tungsten carbide, lates... more
Carbide Shelling Molding Dies Established in 1999, Zhu Xun Precision Mold and Die Factory meets customers’ rapid and large demand with its profound knowledge of tungsten carbide, lates... more
Carbide Shrink Tube Mould Established in 1999, Zhu Xun Precision Mold and Die Factory meets customers’ rapid and large demand with its profound knowledge of tungsten carbide, lates... more
High Precision Tungsten Carbide Shaped Dies Established in 1999, Zhu Xun Precision Mold and Die Factory meets customers’ rapid and large demand with its profound knowledge of tungsten carbide, lates... more
Working with carbide in the fabrication and running stamping dies is really not that difficult. The reluctance to use carbide is usually found in the cost, the machining, and possibly the perception of extended maintenance hours.
Carbide far outweighs the cost in improved performance. Carbide can be readily machined into shapes utilizing the wire EDM process. Some precaution needs to be taken when machining carbide as outlined in the following pages.
The finish is critical in having success running carbide dies. It is a good practice to lap or polish the carbide surfaces, especially cutting edges. It is also advantageous to break or polish the actual cutting edges smooth with a diamond lap. This will help prevent premature chipping.
Another critical factor is tool line up and press condition. Running a properly lined up tool in a poor running press will not work for long, and vice versa.
Carbide punches and dies can extend production runs greatly.
We improve your metal stamping product from the early engineering phase through production and inspection. We address part and tool design concerns head-on, guaranteeing quality and defect-free production.
Expert-Level Consultation and Design Assistance including:
- Engineering drawing analysis
- Design feasibility reviews
- Functionality assessments
- Confirmation of supply tolerances, cost ratios, and other important project considerations
- Informed recommendations about when to use stamping versus other technologies
Requirement Review and Recommendations:
- Part description
- Estimated annual usage (EAU)
- Project lifespan of part
- Special assembly requirements
- Packaging
- And more
Whether you are seeking simple or complex metal stampings and tools, we combine our years of design and precision metal stamping experience to meet low or high volume production requirements. Zhu Xun stamping will work with you every step of the way, providing exceptional service to match your specific tooling design and manufacturing design needs.
Not sure your products requirements? Directly send us all the information you know(CAD/3D drawing/Solid picture), the engineer team will provide the best solutions. Contact us now!
Previous :
High Precision Tungsten Carbide PartsNext :
Metal Parts Stamping Tungsten Steel PG Punch ProcessingEmail us with any questions or inquiries or use our contact data. We would be happy to answer your questions.